Check out these molds make maker china images:
Stokes Croft – Historical Bristol Street Directory 1871
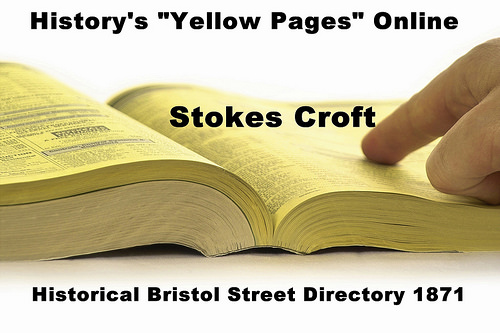
Image by brizzle born and bred
Mathews’ Bristol Street Directory 1871
Stoke’s Croft, North Street to Cheltenham Road
www.flickr.com/photos/brizzlebornandbred/5063962403/
One of the shops which was demolished was where Arthur Holborn ran his photography business for about 40 years. He specialised in portraits which bore his elegantly engraved advertisement on the back. Four doors away art of a different type was produced by Thomas Colley, who was a sculptor and his specialities were ‘monuments, headstones, crosses and memorials of all descriptions’. www.flickr.com/photos/brizzlebornandbred/6174492981/
1. H. Lester, register oflice for servants
2. Richard Pearce, teacher of music
3. William Hagen, painter
4. Oliver Sheppy, family grocer
5. William Corbett
6. Miss Jennings, milliner
7. Walton King, wine & spirit merchant
8. J. Bennett, plumber
9. John Rice, teacher of dancing
10. Thomas Colley, sculptor
11. Benjamin Hamilton, music warehouse
12. Miss Moulding, dress maker
13. Mrs W. Cook, teacher of music, etc
14. William James
15. J. Dilke, house painter
16. George Poole, dentist
17. J. F. Davis, undertaker, etc
18. Richard F. Jones
19. Capt. John Way
20. Mrs Broad
21. Joseph Richards, carpenter
22. Richard Slade, painter, etc
23. James Webber
Brooks Dry Cleaners Ltd St Werburghs Bristol www.flickr.com/photos/brizzlebornandbred/2046815682/
24. Henry Bishop, Bevan, vict, Antelope (pub) 1837 – 44 John Thomas / 1847 – 59 William Salter / 1860 – 63 Ann Salter / 1865 – 66 James Ricketts / 1867 – 69 Andrew Lewis 1871 – 76 Henry Bishop / 1877 to 1878 T. Gall / 1879 Charles Tovey & Co. / 1882 – 83 Thomas Sedgebeer / 1885 Eliza Perry 1886 J. Machan / 1887 to 1888 George Thomas Mills / 1889 Charles George / 1891 William Northam / 1892 – 96 Henry Burrow 1899 Thomas White / 1901 Nellie Jenkins.
In the 1880s the consecutive numbering system of Stokes Croft changed to odds on one side, evens on the other. In 1873 Charles Board cabinet maker and billiard table manufacturer was listed at no 20. He was still in the same premises as a billiard table manufacturer in 1906, but it was now no 37. Next door (building in scaffolding) had three different occupiers between 1873 and 1906 – Joseph Richards, carpenter had gone by 1888, replaced by Staffordshire Supply Store and by the 1900s Wall and Co, furniture dealers.
25. G. Evans, flour dealer
26. Waters & Co. wine & spirit merchants
27. William Pepper, hosier, etc
27. Thomas Crew, porter stores
28. James Brown, baker
29. William Thomas
30-31. William Merson, saddler
Charles Latham, attorney
31. John Milton, venetian blind maker
33. William Robins, painter, etc
34. www.flickr.com/photos/20654194@N07/10383609634/
36. www.flickr.com/photos/brizzlebornandbred/9280249203/
39. James Morse & Co. grocers
www.flickr.com/photos/brizzlebornandbred/10380679115/
40. George Stallard Nipper, builder
41. William Chapman, painter, etc
42. Selina Chapman, earthenware dealer
43. Charles Phillips, greengrocer
44. Charles Williams, boot maker
44. Theodore May, dyer
45. Nathan Palmer, soap and candle dealer
www.flickr.com/photos/brizzlebornandbred/10381070043/
46. Thomas Prewett, baker
47. George Gillingham, painter, etc
48. T. W. Lansdown, greengrocer
49. Edward Brown, greengrocer
50. George Pymm
51. John Sprod, grocer
52. Ann Warley, greengrocer
53. Daniel Taylor, smith and bell hanger
54. William Holbrook, fishmonger and poulterer
55. J. C. Hewitt, goldsmith & jeweller
56. Mary Tossell, vict, Little Swan (pub) 1848 – 66 John Tossell / 1866 – 72 Mary Tossell / 1874 – 89 John Jenkins Eastman / 1890 Clara Eastman / 1891 Clara M. Symes 1892 to 1893 Martha Street / 1894 – 1901 Donald Barry / 1904 – 09 George Rexworthy / 1914 Bridget Spencer / 1917 – 25 Albert Alder 1928 – 31 Alfred Scott / 1935 – 37 Jeremiah McCarthy. www.flickr.com/photos/brizzlebornandbred/
57. Charles Taylor, hair dresser
58. William Rokins, greengrocer
58-76 Stokes Croft www.flickr.com/photos/brizzlebornandbred/10383296583/
59. James Hewitt, vict, Swan Hotel Near the corner with Nine Tree Hill the Swan Hotel is still trading, but is now known as the Croft. bristolslostpubs.eu/page195.html
60. Charles Davis, confectioner
Vincent Skinner, horticultural builder
Tucketts Building
On the corner of Ashley Road stands 108, Tucketts Buildings an ebullient example of late Victorian commercial premises. It is said that human bones were dug up in the foundation trenches, probably from the victims of the gallows which once stood here.
The Tuckett’s Buildings 108 Stokes Croft sweep around the Ashley Road corner.
Named after Coldstream Tuckett who developed the site and opened his grocery and provisions shop there in the 1890s. During the excavations two skeletons were found. It was suggested that they were 17th/18th century suicides who, according to the custom of the time, had been buried at the crossroads.
F. Coldstream Tuckett had his grocer’s shop in part of this building until about 1920. He was a member of the Executive Committee of the Bristol & District Grocers’ & Provision Dealers’ Association. When the Grocers’ Federation of the United Kingdom held their Summer Conference in Bristol in July 1900 he was Press Steward and half of the two-man Entertainment Committee.
In 1911 two boys named Cooper and Hardwick were charged at Bristol Police Court with breaking into his premises through Skinners Yard at the back. They stole a bottle of port and some pork pies. The court sentenced them to a birching.
Although a route through Stokes Croft is likely to have existed for centuries earlier, the first reference is in a deed of 1579. The land is recorded as a field containing one little lodge, a garden and pasture, with a footpath running through the grounds. In 1618, the city received 6d for mending holes in the stile.
61. T. J. & J. F. Perry, carriage builders
62. Charles S. Davey, corn and flour dealer
63. Pugh and Son, grocers
64. James Kebby, butcher
65. M. A. Alexander
66. John Smith, porter stores
67. Isaac Thomas, bookseller
68. Thomas Mann, tailor
69. J. Sampson, boot maker
70. James Melhuish, pork butcher
71. E. J. Hatherley, builder, Stokes croft house www.flickr.com/photos/brizzlebornandbred/6174888582/
72. Edwin Peacock, chemist
Baptist College – Rev. Dr. Gotch
73. Joseph A. Cortisi, confectioner
73. George Park, toy warehouse
76-74 Stokes Croft www.flickr.com/photos/brizzlebornandbred/10382901475/
74. John Parry, boot maker
75. J. Greenham, tobacconist
76. Misses Wallington, fancy repository
www.flickr.com/photos/brizzlebornandbred/10381417373/
77. Miss E. Wallington, milliner
78. J. Cluett, china warehouse
(North Parade)
6. A. Willis, butcher
5. Eleanor Ford, fancy draper
4. Robert G. Whiting, boot maker
3. George A. Peacock, fishmonger, etc
2. S. Palmer, spirit dealer
1. John Howe, boot maker
1. W. Greening, druggist
(City Road Intersect)
Foll and Abbott, Stokes Croft Brewery www.flickr.com/photos/brizzlebornandbred/10383594583/
77. Charles and Wakefield, tailors, etc
78. George Nelson Naish, boot maker
www.flickr.com/photos/brizzlebornandbred/10381553633/
79. W. H. Hawkins, plasterer & painter
80. S. Bruton, music warehouse
81. Henry O. Richards, boot maker
82. Robert Tyler, wine & spirit merchant www.flickr.com/photos/brizzlebornandbred/10380482016/
83. J. W. Sane, ladies’ outfitter
83. Frederick Calder, confectioner
84. Anthony Power, berlin and fancy depository
85. W. J. Exon, baker www.flickr.com/photos/brizzlebornandbred/6174410583/
86. Charles Tovey & Co, wine merchants
87. A. M. Withers, ironmonger
88. Francis Virtue, bookseller
89. John Parnall, ladies’ outfitter
90. Unitarian Almshouses & School
Stokes Croft School www.flickr.com/photos/brizzlebornandbred/2049372251/
91. Isaac Simmonds, plumber, etc
92. John H. Diggs, tobacconist
93. Sarah Mountjoy, fancy depository
94. George King, grocer
95. Edward Hunt, ironmonger, etc
Walter James Hooper & Co. fish and poultry market. www.flickr.com/photos/brizzlebornandbred/10381994874/
97-99. www.flickr.com/photos/brizzlebornandbred/10381685406/
101. The Post office www.flickr.com/photos/brizzlebornandbred/10382010883/
Stokes Croft Court, 28, Stokes Croft
Stoke’s Croft Place, Stoke’s Croft
Mrs Spurse
Catherine Parsons
Alfred Jones
John Weeks, 2, Vine cottages
W. C. R. Bailey, 1, Vine cottages
Mrs Duance
John Pottow, farrier
Notes
Ann Barnes – Wife of Mr Barnes wheelwright living near Stokes Croft turnpike Died January 11th 1816 in 22nd year of her age of consumption.
William Chaffe 1753 Died ‘of lunacy’ Inquest held at Full Moon, Stokes Croft
Joseph Church of Newfoundland Gardens, fell down a flight of steps in Stokes Croft in December 1847 and fractured his leg. Admitted to Bristol Infirmary.
Mr Fry Schoolmaster of Stokes Croft married Mrs Dickson of Broad Street at St James’ Church on Friday Nov 7th 1766.
Joseph Glascodine 1793 carpenter and millwright, Stokes Croft.
Edward William Godwin 1833-1886 Born at 12 Old Market Street, alter living at 21 Portland Square. One of his best-known designs is the Carriage and Harness Factory in Stokes Croft.
George Longman of Stokes Croft., married Mrs Mary Clampit of Catherine Place February 3rd 1829.
William Morgan – Recommended for receipt of parish relief (St James) in 1814. He was a tailor with a wife and 4 children who had worked for John Rice of 23 Stokes Croft for some years. Rice could no longer employ him due to ‘work being dead’.
Henry Parker, cab driver, he was charged at Bristol Police Court in January 1899 with ‘furious driving’ in North Street and Stokes Croft. As he had been in trouble before he was fined 10s and costs.
Samuel Parry (d. 1839) Aged 88, of Stokes Croft was buried at St Paul, Portland Square on January 20th 1839.
James Sadler 1753-1828 Originally from Oxford where his family had a confectionery business. Interested in engineering and chemistry. Made several balloon flights before his ascent from Stokes Croft in Bristol on September 24th 1810., accompanied by William Clayfield Watched by a large crowd the balloon rose up and was carried over Leigh Down, where they dropped a cat in a basket attached to a parachute. (The cat was rescued by a watching limeburner. The balloon eventually landed in the Bristol Channel near Lynton.
John Stoke, Mayor 1364, 1366 and 1379. His will was proved in 1382. Stokes Croft, originally known as Berewyke’s Croft was named after him.
Isaac Van Amburgh, Lion tamer, who gave an exhibition at Bristol Zoo in July 1839 and met with an ‘accidental injury whilst thrusting his hand into a lion’s mouth’. A newspaper report stated that he was completely recovered and would give some more performances before continuing with his tour. This was no means his only visit to Bristol. In August 1842 there were newspaper reports of how he ‘made an entrance into the city driving 8 beautiful cream coloured horses in hand’. The procession of vans was accompanied by an elephant. And made its way to Backfields, Stokes Croft where a spacious pavilion was erected.
Archy Walters, Elder of two young brothers who walked from Stokes Croft to Horfield and lost their way in the fields as night fell. As it grew colder and colder they took shelter under a hedge and Archy wrapped his brother in his own clothes to keep him warm. They were found next morning, but too late to save Archy, although his brother survived thanks to his selfless act.. References: Memorial stained glass window in Horfield Parish church,
Wimble (d. Nov 1766) Died at his house in Stokes Croft.
Schools
Misses Armstrong’s Boarding School for Young Ladies, Wellington Place, Stokes Croft Listed 1847.
Mrs Baker’s School for Ladies, 4 Wellington Place, Stokes Croft. Mrs Baker gave the establishment her ‘strict personal attention’ according to newspaper notice of 1830 which stated that teaching was ‘conducted on a plan approved by men of learning which renders abstruse studies comprehensible and entertaining’.
Churches
Stokes Croft Chapel, Stokes Croft (Christian Brethren) This was originally a skating rink and was purchased on 8th July 1879 by the ‘friends worshipping in Bethesda Chapel and Salem Chapel St Augustine’. It was fitted up as a place of worship in lieu of Salem, which was then vacated. It accommodated 500 people and was ‘neatly fitted up at the expense of £500-600’.
Businesses
Wyndham Lewis, 102 Stokes Croft Baker and Confectioner.
Massingham – Red House Boot Stores, 77 Stokes Croft. trading in 1901.
W E Pritchard, 95 Stokes Croft. Fishmonger & Poulterer. Trading in May 1901.
E K Vaughan, 56 Stokes Croft, Jeweller and Watchmaker Trading May 1901.
New Zealand quotations (3)
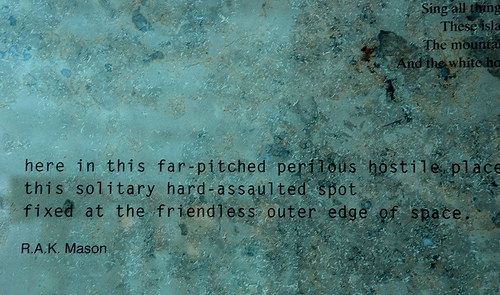
Image by PhillipC
Ronald Allison Kells Mason was born in Penrose, Auckland, on 10 January 1905, the son of Francis William Mason and his wife, Jessie Forbes Kells. His father, a perfume maker, died of an accidental overdose of opium in 1913 and he and his elder brother were sent to live with an aunt, Isabella Kells, in the south Waikato settlement of Lichfield. She taught the boys until 1915, when Mason returned for one year’s primary schooling at Panmure before attending Auckland Grammar School from 1917 to 1922 (in 1919 and 1921 for only one term each year, apparently for economic reasons). He distinguished himself in English and Latin, and began writing verse. His translation of Horace’s ‘O fons Bandusiae’ (‘O fair Bandusian fountain’) was evidently a class exercise done in the fifth form. In that same year he first encountered A. R. D. Fairburn, with whom he formed a close association over the next decade.
Soon after leaving school Mason took a position as a tutor in Latin, economics and civics at the University Coaching College, a private tutoring school where he was to be employed for six years. In 1923 he prepared a handwritten collection of poems which he named ‘In the manner of men’. This was followed in 1924 by his first published volume, The beggar , which contained versions of many of the poems written during his school years. They are precocious, often morbid poems that reflect the highly rhetorical styles of the Victorian poets, but some are of lasting value. The beggar found almost no market in New Zealand. It did, however, reach the English anthologist and editor Harold Monro, who reprinted two of its poems in the 1924 issue of the Chapbook , and two more in the 1929 anthology Twentieth century poetry .
In 1925 Mason published a pamphlet, Penny broadsheet , containing five further poems. In 1926 he enrolled at Auckland University College, majoring in Latin and French. He studied full time that year and from 1928 to 1930, eventually graduating BA in 1939. Mason evidently continued to support himself by tutoring until near the end of his full-time studies. He continued to write poems, some of which were published in the local newspapers, the Sun and the Auckland Star , and wrote several short stories, published in Kiwi , the Phoenix and Tomorrow ; He also drafted two novels, which remained unpublished.
After completing his full-time studies he worked for a season in Lichfield as a harvester before returning to Auckland to a variety of labouring jobs, and to close association with friends active at the university. In the first months of 1931 he travelled to Tonga and Samoa to study the conditions on those islands, and particularly the circumstances of the Mau uprising in Samoa. This trip he described as beginning his disillusionment with New Zealand nationalism, which was to culminate in 1947 with the publication of the pamphlet Frontier forsaken: an outline history of the Cook Islands .
Between 1931 and 1933 Mason contributed regularly to Kiwi and to the Phoenix , a student publication printed by Bob Lowry at Auckland University College. The first two issues in 1932, edited by James Bertram, emphasised cultural and aesthetic issues. Mason assumed the editorship in 1933; under him the third and fourth issues had a more directly political emphasis, and the magazine’s controversial nature made it the focus for attack from the conservative press.
By this time Mason’s interests had clearly moved from the poetic to the political. Although he was to publish three books of verse in the next 10 years, all but about 12 of the poems eventually collected under his name had been written by 1933. No new thing (1934) contained 25 poems from 1924 to 1929. The book was printed by Lowry at the Unicorn Press, but problems with binding meant that only a few copies were issued for sale. Mason retained his business association with Unicorn for a short time, but the Caxton Press published his poems from then on. End of day (1936) printed five new poems, and a further five were included in Caxton’s Recent poems (1941). This dark will lighten: selected poems, 1923–41 was Mason’s first substantial selection of his work and the first to make it widely available. In it he stripped down the typography and punctuation, making increasing use of the hanging indent that he had first used a decade before, and paring down the rhetorical diction and flourishes of some of the earlier poems.
Mason’s writing after the mid 1930s was mainly political journalism and didactic plays for the stage, radio and dance theatre. At least 10 plays were written; two were published separately, Squire speaks in 1938 and China: script…for a dance-drama by Margaret Barr in 1943. He wrote political and social commentaries extensively, using both his own name and ‘PWD’. He published in Tomorrow , the Workers’ Weekly and the People’s Voice , the communist weekly newspaper. When this was banned by the government in 1941, Mason edited, printed and published its successor, In Print. He was briefly the publisher of the revived People’s Voice in 1943–44 and then publisher of Challenge , the weekly journal of the Auckland District Labourers’ Union. He is also recorded in 1950 as the publisher of a union paper, Congress News , the journal of the New Zealand Trade Union Congress. He made another trip to the Pacific islands prior to the publication of Frontier forsaken in 1947. In the years immediately after the war he was a strong advocate of the establishment of a national theatre.
Ill health forced Mason into semi-retirement in 1956, though for several years he continued to work a little as a landscape gardener. In that year he welcomed a troupe of the Classical Theatre of China to Auckland, and in 1957 he was a member of a New Zealand delegation invited to the People’s Republic of China.
In 1962 Pegasus published his Collected poems. The book drew together all the published and unpublished poems he wished to retain, while the last of the earlier poems were revised for republication. In the same year he held the Robert Burns Fellowship at the University of Otago. Three poems were printed in the students’ association’s Review and ‘Strait is the gate’, a play with strong Otago themes, was performed and later recorded for radio. Also that year, on 27 August, he married his long-time companion Dorothea Mary Beyda (known by her maiden name of Dorothea Mould). They remained in Dunedin until 1965, when they returned to Auckland, living in Takapuna where Mason taught part time. In 1969–70 the New Zealand Literary Fund Advisory Committee discussed a recommendation that a pension be paid to him in recognition of his achievements, but he died on 13 July 1971 before this could be done. He was survived by his wife.
In his own lifetime Mason was respected for his commitment to the trade union movement, and for his dedication to the principles of Marxism as a political philosophy. Although it is as a poet that he is deservedly best remembered, the ethical and existential questions that the poems confront seem to have been answered for Mason by his espousal of Marxist principles, and the transferral of energy from poetry to politics in the mid 1930s was a part of this process. Mason’s poetry was humanistic and sceptical, concerning itself with the quest for purpose in a universe which appeared to be essentially mechanistic or godless. The earlier poems are frequently concerned with a sense of despairing mortality, and a feeling that the poet is the plaything of history. The later poetry, often focusing on the figure of a secular suffering Jesus, who is human rather than divine, poses dramatised questions about the consequences of ethical choice and the problems faced by the good man in a morally indifferent society.
Stylistically and thematically much of Mason’s poetry marks him as an inheritor of the Victorian tradition, although equally he was influenced by the Georgian practices of his time. His work stands somewhat apart from the more overtly nationalistic writings of his contemporaries, though he shared with them a sense of romantic alienation and a view of poetry as primarily a morally instructive art. His poems from The beggar on also mark the beginnings of serious modern poetry in New Zealand, and his best poems remain numbered among the finest in New Zealand literature.
Benn & Adelaide Pitman Bedstead
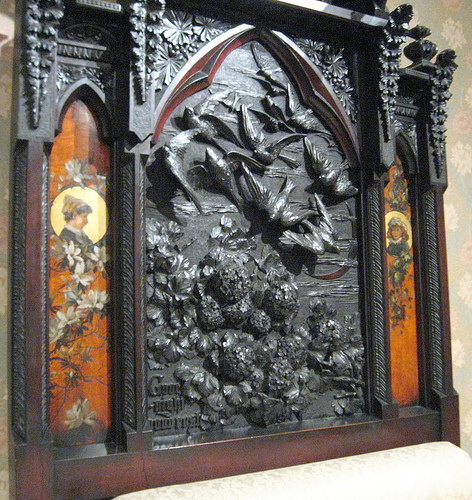
Image by elycefeliz
www.discoveringthestory.com/goldenage/bed/background.asp
This mahogany bedstead was designed by Benn Pitman on the occasion of his marriage to his second wife, Adelaide Nourse. Adelaide carved the decorative motifs on the bed, which was made for the Pitman home on Columbia Parkway. The interior of the home was decorated with carved floral and geometrical motifs based on native plant life. Everything in the home was carved by hand, from the baseboards to ceiling moldings and all its furniture.
The bedstead is Modern Gothic in style and is composed of a headboard, footboard, and two side rails. The headboard is divided into three sections: two lancet panels with egg molding and a central trilobate arch. The central panel is carved with a flock of swallows flying in the evening sky. The birds are depicted in various stages of relief, some nearly four and a half inches from the headboard. Others are shown in low relief to suggest a sense of depth. Just below and to the right of the birds is a crescent moon in low relief. Hydrangea blossoms in high relief are carved into the lower section of this panel. In the lower left is a carved inscription that reads, "Good night, good rest." Extending above this is an arched hood that is carved with four panels of overlapping daises. The four finials of the headboard are carved in the shape of wild parsnip leaves.
In the two lancet panels on either side are painted images of human heads on gold discs representing night and morning. These panels were painted by Elizabeth Nourse (1859-1938), Adelaide’s twin sister, who was an internationally acclaimed painter. To the left is Morning, surrounded by painted white azaleas. To the right is Night, surrounded by balloon vines. The corners of these side panels are carved with stylized leaves and berries.
This bed, which occupied the Pitman’s bedroom, was meant to symbolize and celebrate sleep. Soon after its completion, it received much acclaim and was exhibited in 1883 by the Pitmans at the Fifteenth Annual Exhibition of the Work of the School of Design of the University of Cincinnati and also at the Cincinnati Industrial Exhibition. In 1909 the bedstead and the rest of the bedroom were described in the Cincinnati Commercial Gazette: "It is such a room in which a sufferer of insomnia would totter drowsily upon entering. The entire combination is made to symbolize "night" and so faithfully is repose portrayed that sleep nearly overcomes one within the door. The bed is a masterstroke of human genius…and the entire combination seems covered with such a consistent nocturnal veil as to make the words "good night" at the bottom quite unnecessary."
72.249.182.183/collection/search.do?id=15453&db=objec…
Artist/Maker Benn Pitman (American, b.1822, d.1910)
Elizabeth Nourse (American, b.1859, d.1938)
Adelaide Nourse Pitman (American, b.1859, d.1893)
Date 1882-1883
Medium American black walnut and painted panels
Credit Line Gift of Mary Jane Hamilton in memory of her mother Mary Luella Hamilton, made possible through Rita S. Hudepohl, Guardian
Benn Pitman, an expatriated Englishman, arrived in Cincinnati from Philadelphia in 1853. Although trained to be an architect, he traveled to America to promote the phonetic shorthand system developed by his brother Sir Isaac Pitman. Sometime between his arrival and 1872, he developed an extraordinary interest and skill in woodcarving. Pitman embraced the Aesthetic Movement and turned to nature for inspiration.
In 1872, carved furniture, doors and baseboards made by the Pitman family, including his wife, Jane, and daughter Agnes, were exhibited at the Third Cincinnati Industrial Exposition.
He taught woodcarving at the School of Design of the University of Cincinnati (later the Art Academy) from 1873 to 1892. He also invented an electrochemical process for relief engraving (1855), was court recorder for the Lincoln assassination trial (1865) and wrote a biography of his brother (1902).
Adelaide Nourse Pitman, the twin sister of Elizabeth Nourse and youngest of ten children, was born on October 26, 1859, in the Cincinnati suburb of Mt. Healthy. Her parents had moved to Cincinnati from Massachusetts in the early 1830s. Her father, a banker, suffered serious financial losses after the Civil War. As a result of this loss, the girls were required to support themselves. The twins enrolled in the University of Cincinnati School of Design, which charged only minimal tuition. While at the University, Adelaide joined Marie Egger’s china painting class and began several years’ study of wood carving under Benn Pitman. She worked on the carving of the Cincinnati Music Hall organ screen, carved a number of architectural elements for the interior of the Ursuline chapel in St. Martin, and received a silver medal at the 1880 Cincinnati Industrial Exposition.
On August 10, 1882, Adelaide married Pitman in Sandusky, Ohio. She was twenty-two and he was sixty. After their marriage, she continued to work, under his supervision, in copper, silver, and brass, as well as on decorative wood carvings for the Pitman home on Columbia Parkway.
In 1883 she gave birth to her first child, who died in infancy. The couple’s second child, born July 5, 1884, was named Emerson. The third and final child born to the couple was their daughter, Melrose, born on November 5, 1889.
Tragically, Adelaide Pitman died on September 12, 1893 of tuberculosis. She was only thirty-three years old.
Elizabeth Nourse was a painter, sculptor, wood-carver, etcher, illustrator and decorative artist who achieved her greatest success after 1887 as an expatriate in Paris. Born a twin in Mount Healthy, she enrolled in 1874 at the Cincinnati University School of Design, graduating in 1881. She had planned to continue her studies in New York, but with the death of her father and the marriage of her sister, Adelaide, to furniture-maker Benn Pitman her plans changed.
Nourse studied for a few months at the National Academy of Design and from 1883-86 worked as a portrait painter spending part of each summer sketching and painting in the mountains of eastern Tennessee. It was the local people who would become her subjects. In 1887 she exhibited four watercolors at the Cincinnati Industrial Exposition and soon after she and her older sister, Louise, left for what was to be a visit to France. They spent the rest of their lives abroad.
www.cincinnatiartmuseum.org/