Choosing the right tool steel is not an easy task. If you picked up the wrong material, it will ruin all your work and will cost you a good monetary loss. Buy the tool steel from a trusted source where you have no doubt about the quality and performance of the product. Choosing the correct mold ensures efficiency and high quality. Choosing the right size before can save the trouble of giving it a finishing.
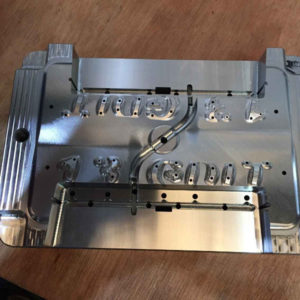
Final production depends upon the type of plastic injection mold material you choose. The selection should be done carefully and the product must be comprised of these qualities. The molded steel must have the strength and bearable because during the injection molding process the mold plates go through a lot of clamping pressure, which if mold is not strong enough then it cannot bear. It must have the strength to perform well. The steel should not have any defects like holes, impurities in order to get the smooth final product. During the molding process, addictive & plastics will release corrosive gases, which the steel should be strong enough to resist.
Tool steels are available in many grades like air-hardening tool steel, water-hardening tool steels, and oil-hardening tool steels; hot-working tool steels, shock-resisting tool steels, high-speed tool steels, etc. There is a variety to choose from. Lots of options may confuse you and trouble you about your selection. Then these tips and hints can help you in selecting the proper object. First of all, keep these things in mind while choosing:
Budget – The choice of steel depends on your budget. If your budget is low, then you can use Water-hardening tool steels, it is a good substitute for cost and mechanical properties. It does not need any other element.
Type P tool – For plastic molding, a special type of tool steel is required. It comes in the Type P of tool steel family. This tool steel is especially for the manufacture of plastic molds or molds for metals with low melting temperatures.
Temperature – Using tool steel at a high temperature is not suggested because it is already heat treated and doing it again may lead to losing its usefulness. For high temperatures, hot work tool steel should be used. They will not use their hardness and are wear resistant even at high temperatures.
Others – For unusual applications also there are special types of tool steels available which are mostly proprietary.
The final product requires high cosmetic requirements. Temperature and climate also play an important role. At high-temperature, mold steel in under the danger of getting oxidized. Through the Electro-Slag-Remelted (ESR) process, you can get the best conditions for cosmetic finishes. It ought to be done carefully. Your final product and its performance depend upon the product you choose and its application. The tool steel should meet above-mentioned requirements and the process of molding should be smoothly delivered. Then only you can get a proper final product with no defects.
If you too are looking for tool steels for your plastic applications, then visit China mold factory. Here you will get all kinds of molding products injection mold, plastic mold, etc. It is the best molding company in China.
The original of this article is from http://www.automoldchina.com.