Some cool high-quality automotive molding images:
Nomination 49 – Materials – Controlled Crystallization Rate to Eliminate Paint
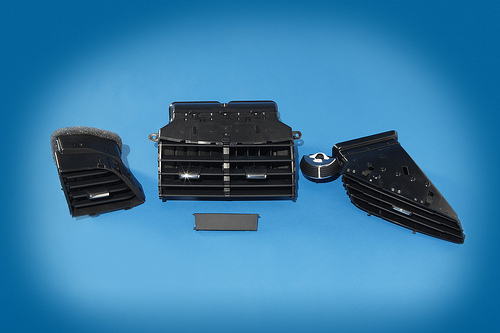
Image by spe.automotive
CONTROLLED CRYSTALLIZATION RATE TO ELIMINATE PAINT
•OEM Make & Model: Ford Motor Co. 2013MY Ford Escape CUV & Fusion® sedan, & Lincoln® MKZ® luxuary sedan
•Tier Supplier/Processor: TRW Automotive, Key Plastics LLC
•Material Supplier / Toolmaker: Asahi Kasei Plastics North America / Liberty Molds, Inc., J&J Tool & Mold Ltd.
•Material / Process: Leona® 90G60 B3374 PA 6/6 / 6I / injection molding
•Description: In order to support greater design freedom for any shape and length register vanes while meeting stiffness, durability, and perceived quality requirements, a partially aromatic injection-molded PA 6/6 / 6I resin was used to boost modulus without increasing wall thickness or adding glass reinforcement to achieve a high-quality, MIC Class A surface without paint. Owing to the "kinked" crystalline structure of the semi-aromatic PA resin, crystallization rate can be better controlled, so parts fully pack out before skins freeze off, leading to a resin-rich surface with a smoother surface and better appearance, eliminating the need to paint.
Extremely rigid construction
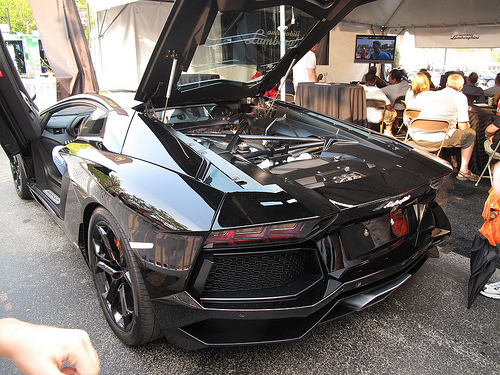
Image by felixdaacat
Superior passive safety is only one benefit of the extreme rigidity of a full carbon fiber monocoque – very high torsional rigidity is another. The monocoque is connected at the front and rear with equally rigid aluminum sub-frames, on which the suspension, engine and transmission are mounted.
The entire body-in-white of the future V12 model weighs only 229.5 kilograms (505 lbs) and boasts phenomenal torsional rigidity of 35,000 Newton meters per degree of twist. This guarantees a superb feeling of solidity, but, more importantly, extremely exact wheel control with excellent steering precision and sensitive feedback. For the dedicated driver, both are essential for truly enticing driving pleasure. The new Lamborghini flagship responds to the most minute steering input with the stunning precision of a perfectly balanced race car.
Depending on the form, function and requirements of the individual elements, the Lamborghini development team selected from three main CFRP manufacturing methods within its technology tool kit. They differ not only in their production processes, but also in the type of carbon fiber and its weave and, most importantly, in the chemical composition of the synthetic resin used.
Resin Transfer Moulding (RTM): In this process the carbon fiber mats are preformed and impregnated with an exact amount of resin. Afterwards, they are cured under heat while the part is in the mould. Lamborghini has achieved a major breakthrough by further developing this method. Using the patented “RTM-Lambo” process, the final mould is no longer a heavy, complex metal piece, but is made instead from lightweight carbon-fiber parts, thus making the manufacturing process faster, more flexible and more efficient.
An additional benefit of the RTM-Lambo process is the low injection pressure that doesn’t require expensive equipment.
Prepreg – The carbon fiber mats used in this method, commonly known as prepreg, are pre-injected by the supplier with a thermosetting liquid resin and must be stored at a low temperature. The mats are then laminated in molds and cured under heat and pressure in an autoclave. Prepreg components are complex to make, but have an extremely high-quality surface finish (Class-A surface quality) and are therefore the preferred option for use in visible locations.
Braiding – These components are manufactured by using RTM technology. This carbon fiber weave technology is derived from the textile industry and used to make tubular components for special applications such as structural roof pillars and rocker panels. The woven components are made by diagonally interweaving the fiber in several layers.
The monocoque of the new V12 super sports car is constructed using these technologies applied in a series of special processes. One significant advancement Lamborghini realized is the ability to use already-assembled monocoque elements as the mould for the next step in the process. This makes for a considerable simplification of the manufacturing process compared with conventional methods.
Epoxy foam components are also used within the monocoque. They are placed in strategic points to increase the stiffness of the monocoque by working as spacers between the composite layers while also dampening noise and vibration. In addition, aluminum inserts are laminated into the front and rear surfaces to facilitate connection with the aluminum front and rear sub-frame elements.
Because of the complexity of the materials and process outlined above, Lamborghini decided to produce its new monocoque completely in-house, managing one strategic step in the production process.
Quality control is an absolutely crucial factor – every single monocoque is measured to exacting tolerances of only 0.1 millimeters, facilitating the extreme precision of the overall vehicle. Quality control starts with the purchase of the carbon fiber parts. Every delivery of carbon fiber is certified and the material is checked regularly for compliance with quality standards. Lamborghini worked together with its suppliers to develop a world-exclusive fiber and resin system for its RTM technology. Ultimately, these materials and processes constitute an important part of Lamborghini’s worldwide leading expertise in the field.
Carbon composite materials – A key technology for tomorrow’s high-performance automotive engineering
These materials made from CFRP combine the lowest possible weight with excellent material characteristics – they are very light, extremely rigid and exceptionally precise.
Furthermore, CFRP materials can also be formed into highly complex components with integrated functions. This reduces the number of individual parts when compared to traditional metal construction – thus enabling further weight reduction. Lighter cars have lower fuel consumption and fewer CO2 emissions. Most significantly, however, it improves the power-to-weight ratio – the deciding factor in the overall feel and performance of a sports car. A super sports car built using CFRP accelerates faster, has superior handling and better braking.